v belt tension chart pdf
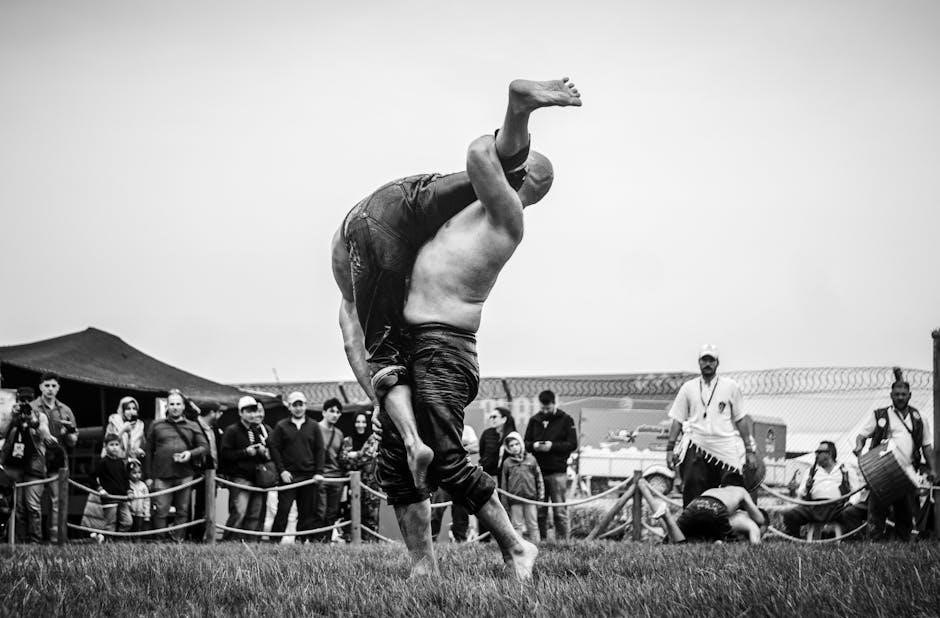
V belt tensioning ensures optimal performance and longevity in power transmission systems․ Proper tensioning‚ guided by a V belt tension chart‚ prevents wear‚ slippage‚ and noise‚ while maintaining efficiency․ Understanding and implementing correct tensioning methods is essential for extending belt life and reducing operational downtime․
1․1 Importance of Proper Belt Tension
Proper belt tension is crucial for ensuring optimal performance‚ longevity‚ and reliability in power transmission systems․ Under-tensioning leads to slippage‚ excessive heat generation‚ and premature wear‚ while over-tensioning can cause stress on bearings and shafts․ Maintaining the correct tension extends belt life‚ reduces operational downtime‚ and prevents unexpected failures․ Using a V belt tension chart ensures accurate adjustments‚ balancing system efficiency and component durability․ Proper tensioning is foundational for achieving consistent power transmission and minimizing maintenance costs․ It is essential for both initial installation and ongoing maintenance routines․
1․2 Overview of V Belt Tension Charts
V belt tension charts are essential tools for determining the correct tensioning parameters for V-belts in various applications․ These charts typically outline recommended tension values based on factors like belt size‚ type‚ and operational conditions․ They often include mathematical standards and deflection guidelines‚ enabling precise adjustments․ By referencing these charts‚ users can ensure optimal tensioning‚ minimizing wear and tear while maximizing efficiency․ Proper use of V belt tension charts helps maintain system performance and extends belt lifespan‚ ensuring reliable power transmission in industrial and mechanical systems․
Methods of V Belt Tensioning
V belt tensioning involves methods like the Force/Deflection and One-Shot techniques‚ utilizing tools such as a pencil gauge for precise adjustments and ensuring optimal belt performance․
2․1 Force/Deflection Method
The Force/Deflection method is a widely used technique for V belt tensioning․ It involves measuring the belt’s deflection under a specific force‚ typically using a pencil gauge tool․ This method ensures the belt is neither too tight nor too loose‚ promoting efficient power transmission․ Proper deflection is determined by the belt’s span length and the recommended tension values from a V belt tension chart․ Accurate measurement is crucial to avoid premature wear and maintain optimal performance․ Regular checks and adjustments are necessary to compensate for belt stretch and material degradation over time․
2․2 One-Shot Tensioning Method
The One-Shot Tensioning Method is a streamlined approach to achieving proper V belt tension in a single step․ Belts are installed with initial slack and then tensioned to 1․25 times the recommended setting force․ After 15-20 minutes of operation under load‚ the tension is checked and adjusted as needed․ This method ensures even tension across all belts‚ minimizing the risk of over-tightening or under-tightening; It is particularly effective for multiple-belt drives‚ providing a quick and accurate way to optimize belt performance and longevity․ Regular follow-up checks are still essential to maintain proper tension over time․
Factors Affecting V Belt Tension
Belt size‚ type‚ material‚ and environmental conditions significantly influence V belt tension․ Operational factors like load‚ speed‚ and pulley alignment also play a crucial role in maintaining optimal tension․
3․1 Belt Size and Type
Belt size and type significantly impact V belt tension requirements․ Larger belts typically require higher tension to handle greater loads‚ while smaller belts need less to avoid excessive stress․ The type of belt‚ such as classical‚ narrow‚ or banded‚ also affects tension specifications․ Different materials and constructions influence how tension is applied and maintained over time․ Consulting a V belt tension chart ensures proper tensioning based on these factors‚ optimizing performance and extending belt life․ Proper selection and tensioning prevent premature wear and operational issues․
3․2 Belt Material and Construction
Belt material and construction play a crucial role in determining tensioning requirements․ Belts made from rubber or synthetic polymers exhibit different stress and flexibility properties․ Wrapped belts‚ with their fabric cover‚ provide durability‚ while raw-edge belts offer precision and resistance to wear․ The construction type influences how tension is distributed and maintained over time․ High-performance belts‚ such as cogged or variable-speed designs‚ require specific tensioning to optimize their unique features․ Consulting a V belt tension chart ensures alignment with material and construction specifications for accurate tensioning․ This prevents overloading and extends service life․
3․3 Environmental and Operational Conditions
Environmental and operational factors significantly impact V belt tension․ Extreme temperatures‚ humidity‚ and exposure to chemicals can alter belt elasticity and tension․ High-speed applications may require tighter tension to prevent slippage‚ while heavy loads demand precise tensioning to avoid belt fatigue․ Operational conditions like vibration or misalignment also affect tension stability․ Adjustments based on these factors ensure optimal performance and longevity․ A V belt tension chart provides guidelines tailored to specific conditions‚ helping maintain the ideal tension for varying environments and applications․ Proper adjustments mitigate risks associated with these external influences․
Tools and Equipment for Belt Tensioning
Essential tools include pencil gauges‚ belt tension checkers‚ and deflection gauges․ These devices help measure and adjust tension accurately‚ ensuring optimal belt performance and longevity․
4․1 Pencil Gauge Tool
The pencil gauge tool is a simple device used to measure belt deflection․ It features a sliding O-ring that aligns with the belt span on a built-in scale․ To use‚ place the tool on the belt span‚ ensuring it’s centered and perpendicular․ Adjust the O-ring to match the recommended deflection value from the V belt tension chart․ This tool is ideal for quick‚ accurate measurements‚ ensuring proper tensioning without over- or under-tightening the belt․ Regular use helps maintain optimal belt performance and extends system life․
4․2 Belt Tension Checker
The Belt Tension Checker is a precise tool for measuring V-belt tension․ It is placed mid-way between pulleys on the belt’s back‚ suitable for multi-belt systems․ The tool helps achieve the desired tension by adjusting until the gauge matches the recommended value from the V belt tension chart․ Available in models like OPTIKRIK 0‚ I‚ II‚ III‚ it caters to different tension ranges․ Regular use ensures optimal belt performance‚ preventing slippage and wear‚ thus extending system life and reducing maintenance needs effectively․
How to Use a V Belt Tension Chart
Using a V belt tension chart involves matching your belt’s type and size to recommended tension values․ Measure the belt span‚ then consult the chart for ideal tension settings․ Utilize tools like a pencil gauge or tension checker to apply the correct force‚ ensuring optimal performance and longevity․ Regular checks and adjustments are necessary to maintain proper tension over time‚ accounting for factors like wear and environmental conditions․ This process ensures efficient and reliable operation of your machinery․
5․1 Understanding the Chart Layout
A V belt tension chart is structured to provide clear guidance for determining proper tension values․ The chart typically includes sections for belt type‚ size‚ and span length‚ with corresponding tension recommendations․ Users can locate their specific belt by cross-referencing these details․ The layout often features tables or graphs‚ making it easy to interpret and apply the data․ Understanding the chart’s organization is crucial for accurately identifying the ideal tension settings for your application․ This ensures precise adjustments and optimal performance of the V belt drive system․
5․2 Determining Recommended Tension Values
To determine recommended tension values using a V belt tension chart‚ identify the belt type‚ size‚ and span length․ Locate these details on the chart to find the corresponding tension value․ The chart provides specific deflection or force measurements for optimal performance․ Use a pencil gauge tool to measure belt deflection‚ ensuring accuracy․ Always refer to the manufacturer’s guidelines for precise settings‚ as improper tension can lead to belt wear or system inefficiency․ This step ensures the V belt operates within its design specifications for maximum durability and efficiency․
Measuring and Adjusting Belt Tension
Measure belt tension by using a pencil gauge tool to check deflection․ Compare the measurement to values in a V belt tension chart PDF for accuracy․ Adjust tension by loosening the motor and moving it to tighten or loosen the belt‚ ensuring optimal performance without over-tightening․ Recheck tension after initial operation as belts may stretch․ Regular checks are essential for maintaining correct tension and system efficiency․ Always refer to the chart for specific guidance on your belt type and size․
6․1 Step-by-Step Measurement Process
Begin by measuring the belt span length between the pulleys․ Use a pencil gauge tool to deflect the belt at its midpoint․ Apply consistent force until the deflection matches the value specified in the V belt tension chart PDF for your belt type․ Record the measurement and compare it to the recommended tension range․ If the deflection is incorrect‚ adjust the motor or pulley alignment to achieve proper tension․ After adjustments‚ recheck the deflection to ensure accuracy․ Repeat the process for each belt in multi-belt systems․ Always refer to the chart for specific guidance․
6․2 Adjusting Belt Tension for Optimal Performance
After measuring‚ compare the deflection to the recommended value in the V belt tension chart PDF․ If tension is too low‚ loosen the pulley and tighten the belt․ For over-tension‚ slightly loosen the belt․ Recheck deflection after adjustments․ Ensure the belt is evenly tensioned across all strands in multi-belt systems․ Proper tensioning minimizes wear and slippage‚ ensuring smooth operation․ Refer to the chart for specific tension ranges and adjustment intervals to maintain optimal performance and extend belt life․
Maintenance and Retensioning
Regularly inspect belts for wear and tension․ Use a tension checker to ensure proper deflection․ Retension as needed to maintain optimal performance and prevent premature wear․
7․1 Schedule for Regular Tension Checks
Regular tension checks are crucial for maintaining V belt performance․ Schedule checks during initial installation‚ after the first 24 hours of operation‚ and every 1‚000 hours thereafter․ Additionally‚ inspect belts whenever unusual noise‚ slippage‚ or vibration occurs․ Use a tension checker to ensure belts meet recommended deflection values from the tension chart․ Consistent monitoring prevents premature wear and ensures efficient power transmission‚ extending belt life and reducing downtime․ Adjustments should be made promptly if tension falls below acceptable levels․
7․2 Signs of Improper Tension and Remedies
Signs of improper V belt tension include slippage‚ excessive noise‚ and uneven wear․ If tension is too low‚ belts may slip‚ causing heat buildup and premature wear․ Over-tensioning can stress bearings and shafts․ Remedies involve checking tension with a belt tension checker and adjusting to recommended values from the tension chart․ Replace belts showing signs of wear or cracks․ Ensure proper alignment and re-tighten belts after initial operation to maintain optimal performance and extend belt life․ Regular inspections and timely adjustments are key to preventing failures․
Common Mistakes in Belt Tensioning
Common mistakes include over- or under-tensioning‚ ignoring belt wear‚ and not using proper tools․ These errors can lead to premature wear‚ noise‚ and inefficiency․ Proper tools and charts are essential to avoid these errors and ensure optimal belt performance․
8․1 Over- and Under-Tensioning Issues
Over-tensioning can lead to excessive stress on belts‚ bearings‚ and shafts‚ reducing system lifespan․ Under-tensioning causes slippage‚ heat buildup‚ and premature wear․ Both issues result in inefficiency and downtime․ Proper tensioning‚ guided by a V belt tension chart‚ ensures optimal performance and extends belt life․ Regular checks and adjustments are crucial to avoid these common mistakes․ Using the correct tools‚ like a pencil gauge or tension checker‚ helps maintain the recommended tension levels․ Ignoring these practices can lead to costly repairs and operational disruptions․
8․2 Ignoring Belt Wear and Tear
Neglecting belt wear and tear can lead to unexpected failures and downtime․ Cracks‚ frays‚ and glazed surfaces signal the need for replacement․ Overlooking these signs can result in slippage and reduced efficiency․ Regular inspections and timely replacements are essential for maintaining optimal performance․ A V belt tension chart aids in identifying proper tension levels‚ preventing premature wear․ Addressing wear issues promptly ensures smooth operation and extends the lifespan of both belts and system components‚ reducing long-term maintenance costs and operational disruptions․ Consistent monitoring is key to sustaining productivity and reliability․
Proper V belt tensioning is vital for system efficiency and longevity․ Using a V belt tension chart ensures accurate adjustments‚ preventing wear and optimizing performance․ Regular maintenance and timely retensioning are essential for extending belt life and minimizing downtime‚ ensuring smooth and reliable operation across all applications․ Adhering to these practices guarantees optimal power transmission and reduces operational costs effectively․ Consistent monitoring and correct tensioning methods are key to achieving long-term system reliability and performance․ By following these guidelines‚ users can maximize their V belt’s service life and maintain peak operational efficiency․ Proper tensioning ensures safety‚ reduces wear‚ and minimizes unexpected failures‚ contributing to overall system durability and productivity․
9․1 Summary of Key Points
Proper V belt tensioning is crucial for ensuring system efficiency and longevity․ Using a V belt tension chart provides precise guidance for achieving optimal tension levels․ The force/deflection method‚ utilizing tools like the pencil gauge‚ is a widely recommended approach․ Maintaining correct tension prevents issues such as slippage‚ wear‚ and overheating․ Regular tension checks and adjustments are essential to sustain performance and extend belt life․ Adhering to these practices minimizes downtime and maximizes operational reliability․ Proper tensioning ensures smooth power transmission and reduces operational costs effectively․
Key points include understanding the importance of proper tension‚ using appropriate tools‚ and following tension charts for accurate adjustments․ Regular maintenance and timely retensioning are vital for optimal performance․ By adhering to these guidelines‚ users can ensure long-term reliability and efficiency in their V belt systems․ Proper tensioning practices contribute significantly to reducing wear‚ minimizing downtime‚ and enhancing overall system durability․ Consistent monitoring and correct adjustment methods are essential for achieving the best results․ This approach ensures safety‚ reduces maintenance costs‚ and prolongs the service life of V belts․
9․2 Final Tips for Effective V Belt Tensioning
Regularly inspect and adjust V belt tension to prevent slippage and wear․ Use a tension gauge for accurate measurements‚ and refer to the V belt tension chart for specific recommendations․ Ensure proper alignment and pulley condition to maximize belt life․ Avoid over-tightening‚ as it can damage bearings and shafts․ Schedule periodic checks based on operational demands․ Replace belts showing signs of wear or cracking promptly․ Maintain a log of tension adjustments for tracking and future reference․ These practices ensure optimal performance‚ reduce downtime‚ and extend the service life of your V belt system․