fisher 667 instruction manual
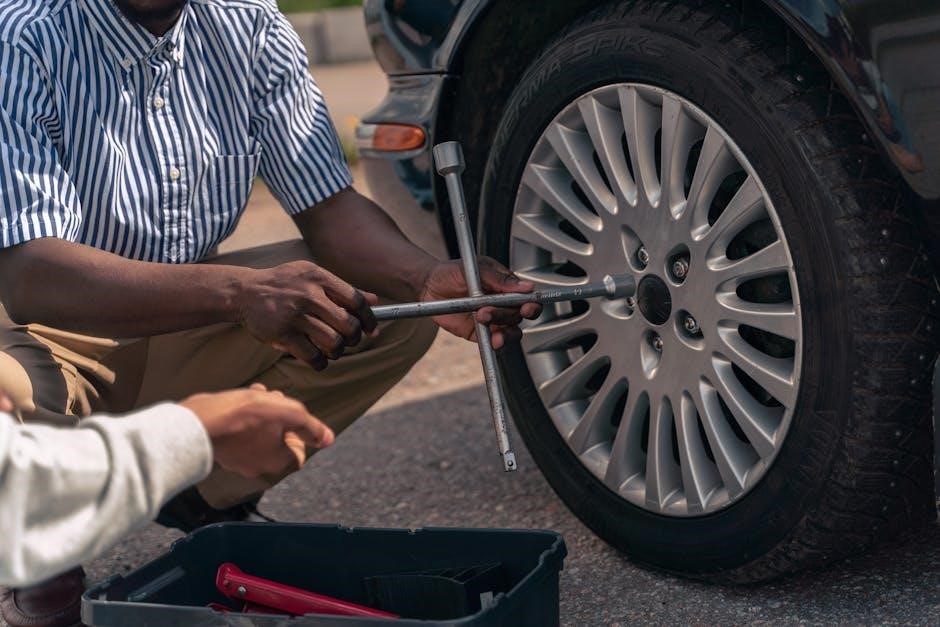
The Fisher 667 actuator is a reliable, high-performance diaphragm actuator designed for automatic valve control in various industrial applications. It offers durability and precise control.
1.1 Overview of the Fisher 667 Actuator
The Fisher 667 actuator is a high-performance diaphragm actuator designed for automatic valve control in industrial applications. Available in sizes 30 through 76 and 87, it ensures precise control and durability. Suitable for oil, gas, and chemical industries, the actuator is known for its reliability and efficient operation, making it a preferred choice for demanding environments requiring consistent performance and long-term durability.
1.2 Importance of the Instruction Manual
The instruction manual is essential for understanding the Fisher 667 actuator’s installation, adjustment, and maintenance. It provides detailed guidance for proper setup and operation, ensuring safety and optimal performance. The manual includes troubleshooting tips and parts ordering information, making it a critical resource for users. Adhering to its guidelines helps maintain compliance with industry standards and prevents potential operational issues, ensuring the actuator functions efficiently and reliably.
Installation and Setup
Proper installation and setup of the Fisher 667 actuator ensure optimal performance and safety. Always follow the manual’s guidelines for compatibility, valve preparation, and correct sizing.
2.1 Pre-Installation Requirements
Before installing the Fisher 667 actuator, ensure the valve is compatible with the actuator size and type. Verify environmental conditions, such as temperature and pressure, meet specifications. Review the instruction manual for compatibility with accessories like positioners and ensure all necessary tools are available. Proper preparation prevents installation errors and ensures safe operation.
2.2 Step-by-Step Installation Process
Mount the actuator to the valve, ensuring alignment and secure fastening. Connect the control signal and power supply according to the manual. Attach accessories like positioners, following torque specifications. Perform a leak test and functional check. Ensure proper alignment and calibration for smooth operation. Refer to the manual for specific torque values and wiring diagrams to avoid errors. Finalize by testing the actuator’s full range of motion.
Adjustment and Configuration
Calibrate the actuator according to the manual, ensuring proper alignment and response. Adjust the control settings to meet operational requirements, following step-by-step guidelines for precise configuration.
3.1 Calibration Procedures
Begin by referring to the Fisher 667 instruction manual for specific calibration steps. Ensure all necessary tools are available. Set the actuator to “calibrate” mode, typically involving a switch or control panel adjustment. Adjust spring tension and air supply pressure according to the manual’s guidelines, using provided gauges for accuracy. Proper alignment with the valve is crucial; use recommended tools or methods for precise positioning. Document each adjustment and final settings for future reference. Prioritize safety by following all precautions, such as disconnecting power sources and wearing protective gear when needed. Conduct a final test to verify smooth operation and accuracy across the actuator’s range of motion. If issues arise, consult the manual’s troubleshooting section for guidance. By meticulously following these steps, the Fisher 667 actuator will achieve optimal calibration and performance.
3.2 Configuring Actuator Settings
Refer to the Fisher 667 instruction manual for specific guidance on configuring actuator settings. Begin by setting the actuator’s stroke length and travel limits according to the valve type and application. Adjust the spring tension and air supply pressure as outlined in the manual to ensure proper actuation force. Configure electronic controls, such as positioners, to match system requirements. Verify alignment with the valve stem and test the actuator’s response to control signals. Proper configuration ensures smooth operation and optimal performance.
Maintenance and Troubleshooting
Regular maintenance ensures optimal performance. Clean the actuator, inspect for wear, and lubricate moving parts. Refer to the manual for troubleshooting common issues like air leaks or misalignment.
4.1 Routine Maintenance Tasks
Perform routine inspections of the actuator’s diaphragm and springs for wear or damage. Clean the exterior to prevent contamination. Lubricate moving parts as specified in the manual. Check and replace seals if necessary. Ensure proper alignment of the actuator with the valve to maintain efficient operation and prevent premature wear. Regular maintenance extends service life and ensures reliable performance.
4.2 Common Issues and Solutions
- Air leakage: Inspect and replace worn or damaged seals. Ensure proper tightening of all connections.
- Misalignment with valve: Adjust the actuator mounting to align correctly with the valve stem.
- Diaphragm wear: Replace the diaphragm if cracks or tears are visible. Lubricate moving parts during reassembly.
- Slow response: Check for air supply blockages and clean filters. Ensure proper lubrication of internal components.
Parts and Accessories
The Fisher 667 actuator supports various genuine parts and accessories for optimal performance. These include diaphragms, positioners, and mounting kits, available through Emerson Process Management.
5.1 Ordering Replacement Parts
To order replacement parts for the Fisher 667 actuator, refer to the specified models and sizes in the manual. Contact Emerson Process Management for genuine parts, ensuring compatibility with your actuator size (e.g., 667, 667-4). Use the part numbers listed in the manual for accurate ordering. Separate manuals may be required for additional accessories or equipment used with the actuator.
5.2 Compatible Accessories
The Fisher 667 actuator is compatible with various accessories, including valve positioners and control systems, to enhance functionality. Refer to the instruction manual for specific compatibility details, such as the 667-4 model; Accessories may require separate manuals for installation and operation. Ensure all components are Emerson-approved for optimal performance and safety.
Safety Precautions
Adhere to safety guidelines in the Fisher 667 manual. Handle electrical components carefully. Follow proper installation and maintenance procedures. Refer to the safety manual supplement for detailed precautions to prevent accidents and ensure safe operation.
6.1 General Safety Guidelines
Adhere to safety guidelines when handling the Fisher 667 actuator. Ensure proper installation and maintenance to prevent accidents. Always wear protective gear. Follow electrical safety protocols. Avoid unauthorized modifications. Regularly inspect for wear or damage. Use approved replacement parts. Keep the actuator clean and dry. Follow shutdown procedures before maintenance. Consult the manual for detailed safety precautions to ensure safe operation and compliance with industry standards.
6.2 Emergency Procedures
In case of emergencies, immediately shut down the actuator and isolate power. Use manual override if necessary. Consult the instruction manual for specific procedures. Ensure all safety protocols are followed to prevent injury or damage. Regular training on emergency responses is recommended. Always prioritize system shutdown and professional assistance if needed to maintain safety and operational integrity.
Technical Specifications
The Fisher 667 actuator is available in sizes 30 to 87, offering durability and precise control for pneumatic or hydraulic applications. Its robust design ensures reliable performance across industrial settings.
7.1 Actuator Sizes and Models
The Fisher 667 actuator is available in various sizes, including models 30, 30i, 76, 76i, and 87. Additionally, the 667-4 actuator is offered in sizes 70 and 87. These models cater to diverse industrial applications, ensuring compatibility with different valve systems and operational requirements. Each size and model is designed to deliver consistent performance and reliability in automatic valve control systems.
7.2 Performance Metrics
The Fisher 667 actuator delivers high performance with precise control and durability. It ensures efficient operation across various industrial applications, maintaining consistent and reliable valve control. Performance metrics highlight its ability to handle diverse operational demands, providing superior actuation for optimal system efficiency and longevity.
Operation and Control
The Fisher 667 actuator ensures smooth operation and precise control of valves, offering reliable performance in various industrial applications and integrating seamlessly with control systems for efficient functionality.
8;1 Operating Modes
The Fisher 667 actuator supports multiple operating modes, including automatic, manual, and test modes, ensuring flexible and precise control of valve operations. These modes allow for seamless integration with control systems, enabling efficient operation in various industrial settings. The actuator’s design ensures smooth transitions between modes, maintaining reliability and performance in demanding environments. Proper mode selection is crucial for optimal functionality and safety.
8.2 Integration with Control Systems
The Fisher 667 actuator seamlessly integrates with modern control systems, including compatibility with HART communication and ValveSight DTM software. This ensures precise control and monitoring of valve operations. The actuator supports both analog and digital communication protocols, allowing easy connection to industrial automation systems. Proper integration enhances operational efficiency and enables real-time data exchange, ensuring reliable performance in various industrial applications;
Compliance and Certifications
The Fisher 667 actuator complies with industry standards and holds certifications, ensuring safety and reliability in industrial applications.
9;1 Industry Standards
The Fisher 667 actuator is designed to meet stringent industry standards, ensuring compliance with safety and performance requirements. It adheres to international norms for reliability and durability, making it suitable for diverse industrial applications. The actuator’s design and manufacturing processes align with recognized certifications, guaranteeing operational excellence and compatibility with global regulations. This compliance ensures the actuator’s safety, efficiency, and effectiveness in various operational environments.
9.2 Certifications and Approvals
The Fisher 667 actuator holds certifications from recognized regulatory bodies, ensuring compliance with global standards. It meets industry-specific approvals for safe operation in hazardous environments. The actuator is certified for use in various applications, adhering to strict quality and safety regulations. Emerson Process Management ensures all certifications are up-to-date, guaranteeing the actuator’s reliability and adherence to international standards.
The Fisher 667 actuator is a reliable and high-performance solution for valve control. Always refer to the instruction manual for optimal installation, operation, and maintenance.
10.1 Summary of Key Points
The Fisher 667 actuator manual provides essential guidance for installation, adjustment, and maintenance. It ensures optimal performance and safety. Users must follow instructions carefully to avoid malfunctions. The manual covers various actuator sizes and models, offering detailed procedures for configuration and troubleshooting. Adhering to the guidelines ensures longevity and reliability of the actuator, making it a crucial resource for operators and technicians working with this equipment.
10.2 Final Recommendations
Always refer to the Fisher 667 instruction manual for specific guidance tailored to your actuator model and size. Regular maintenance and adherence to safety protocols ensure optimal performance and longevity. For complex adjustments or troubleshooting, consult Emerson Process Management resources or certified technicians. Proper installation and configuration are critical for reliable operation, and ordering genuine replacement parts is highly recommended to maintain actuator efficiency and safety standards.