lycoming io 360 overhaul manual
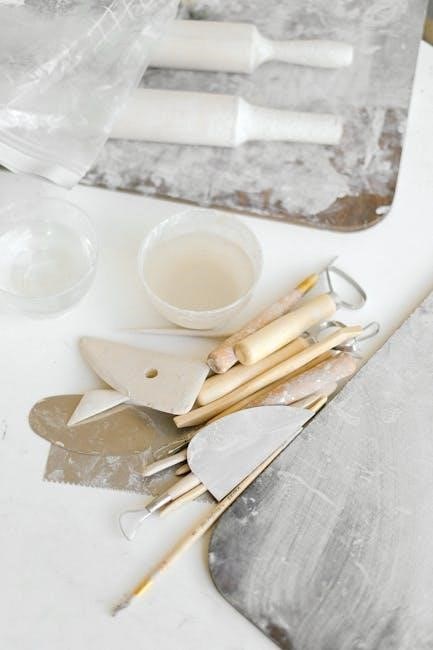
The Lycoming IO-360 is a four-cylinder, fuel-injected aircraft engine known for its reliability and efficiency in general aviation. Regular overhaul ensures optimal performance, safety, and compliance with aviation standards. This guide provides a comprehensive overview of the overhaul process, highlighting key steps, tools, and best practices to maintain the engine’s integrity and longevity.
1.1 Overview of the Lycoming IO-360 Engine
The Lycoming IO-360 is a four-cylinder, horizontally opposed, fuel-injected aircraft engine, renowned for its reliability and efficiency; Introduced in 1962, it produces between 180 to 200 horsepower, making it a popular choice for general aviation aircraft. Its fuel injection system enhances performance and fuel efficiency compared to carbureted engines. Known for durability, the IO-360 powers various single and twin-engine aircraft, ensuring smooth operation and longevity with proper maintenance.
1.2 Importance of Regular Overhaul
Regular overhaul of the Lycoming IO-360 engine is crucial for ensuring safety, performance, and compliance with aviation standards. It prevents wear and tear, identifies potential failures early, and maintains airworthiness. Overhaul also ensures compliance with FAA regulations and extends the engine’s lifespan. A well-maintained engine retains value, reduces operating costs, and provides peace of mind for pilots and aircraft owners.
Understanding the Overhaul Manual
The Lycoming IO-360 overhaul manual provides detailed instructions for major repairs and replacements, ensuring compliance with aviation standards and engine longevity. It is essential for maintenance personnel to follow the guidelines to guarantee safety and optimal performance.
2.1 Structure and Content of the Lycoming IO-360 Overhaul Manual
The Lycoming IO-360 overhaul manual is structured to guide users through major repairs and replacements. It includes detailed sections on inspection, disassembly, and reassembly procedures. The manual also covers parts identification, torque specifications, and safety protocols. Proper use ensures compliance with aviation standards, maintaining engine performance and longevity. Adherence to the manual’s guidelines is crucial for successful overhauls.
2.2 Key Sections and Guidelines
The manual outlines essential sections, including inspection procedures, parts specifications, and torque values. It emphasizes safety measures and compliance with aviation standards. Clear instructions guide mechanics through critical tasks, ensuring accuracy and adherence to best practices. Proper documentation of each step is mandated to maintain traceability and accountability during the overhaul process.
Pre-Overhaul Preparation
Pre-overhaul preparation involves gathering the manual, reviewing engine specifications, and organizing tools. Ensure compliance with aviation standards and prepare for thorough inspection and cleaning of components.
3.1 Tools and Equipment Required
A Lycoming IO-360 overhaul requires specialized tools, including torque wrenches, micrometers, and ring compressors. Essential equipment includes a workbench, vise, and cleaning tools like ultrasonic cleaners and chemical solvents. Additional tools like piston pin pullers and bearing extractors may be necessary for specific tasks. Ensure all tools meet aviation standards for precision and safety. Refer to the manual for a comprehensive list of required tools and equipment.
3.2 Workspace and Safety Considerations
A clean, well-lit, and ventilated workspace is essential for a successful overhaul. Ensure the area is free from hazards and flammable materials. Use proper safety equipment, including gloves and safety goggles, when handling tools and chemicals. Organize tools and parts to avoid misplacement or damage. Employ jack stands or engine mounts to stabilize the engine during disassembly. Always follow proper safety protocols to prevent accidents and ensure compliance with workshop standards.
The Overhaul Process
The overhaul process involves a detailed inspection, disassembly, cleaning, and replacement of worn or damaged parts, followed by precise reassembly and thorough testing to ensure optimal performance.
4.1 Inspection of Engine Components
The inspection of engine components is a critical step in the overhaul process. Each part must be meticulously examined for wear, damage, or corrosion. The crankshaft, camshaft, and cylinders are key areas of focus. Measurements are taken to ensure all components meet factory specifications. Any parts found to be outside acceptable tolerances or showing excessive wear must be replaced to maintain engine reliability and performance. This thorough evaluation ensures the engine operates safely and efficiently post-overhaul.
4.2 Disassembly and Cleaning
Disassembly of the Lycoming IO-360 engine requires careful removal of components, starting with external accessories and progressing to internal parts. Each component is cleaned using approved solvents and methods to remove dirt, oil, and contaminants. Media blasting may be used for heavily soiled parts. Cleaning ensures accurate inspection and prevents reassembly of dirty or damaged components, which could compromise engine performance and longevity.
4.3 Replacement of Worn or Damaged Parts
During overhaul, all worn or damaged parts are replaced with new or rebuilt components. Critical areas include piston rings, bearings, and valves. Crankshaft and camshaft wear are assessed, and replacements are made if beyond limits. Cylinders are inspected for scoring or excessive wear, with liners replaced as needed. Replacement ensures compliance with manufacturer specifications and guarantees optimal engine performance and longevity post-overhaul.
4.4 Reassembly and Alignment
Reassembly requires precise alignment of components, adhering to torque specifications and manufacturer guidelines. The crankshaft and camshaft are carefully installed, ensuring proper mating with bearings. Piston rings are fitted, and cylinders are reattached. Alignment of gears, valves, and other critical parts is verified to maintain engine balance and efficiency. Proper reassembly ensures smooth operation, minimizing vibration and wear, and maximizing engine performance and lifespan.
4.5 Final Testing and Quality Control
After reassembly, the engine undergoes rigorous testing, including static RPM checks, fuel flow verification, and ignition system testing. Leaks, unusual noises, and performance metrics are closely monitored. Compliance with the Lycoming IO-360 overhaul manual ensures adherence to specifications. Final quality control checks confirm proper function and safety, ensuring the engine meets operational standards before return to service.
Post-Overhaul Maintenance
Proper post-overhaul maintenance ensures the Lycoming IO-360 engine operates efficiently. This includes break-in procedures and adhering to scheduled maintenance intervals to maintain performance and longevity.
5.1 Break-In Procedures
After an overhaul, the Lycoming IO-360 engine requires a structured break-in process. This involves gradual operational stress to seat new parts properly. Initial flights should maintain moderate power settings and engine speeds. Avoid extreme temperatures and rapid throttle changes. Proper break-in ensures optimal performance and longevity of the engine components. Compliance with the manual’s guidelines is essential for reliability and safety.
5.2 Scheduled Maintenance Intervals
Adhering to scheduled maintenance intervals is crucial for the Lycoming IO-360 engine. Regular inspections at 100-hour intervals and oil changes every 50 hours are essential. The time between overhauls (TBO) is typically 2,000 hours, depending on usage and conditions. Compliance with these intervals ensures engine longevity, prevents unexpected failures, and maintains airworthiness. Proper documentation of all maintenance activities is required for regulatory compliance and operational safety.
Common Issues and Troubleshooting
Common issues during Lycoming IO-360 overhaul include crankshaft wear, oil leaks, and cylinder damage. Early detection and repair are vital to ensure engine reliability and safety.
6.1 Identifying Common Problems During Overhaul
During the Lycoming IO-360 overhaul, common issues include excessive wear on the crankshaft, premature cylinder wear, and oil leaks from worn gaskets or seals. Inspecting components for these signs early can prevent costly repairs. Proper diagnostic tools and adherence to the manual’s guidelines are essential for identifying and addressing these problems effectively before reassembly.
6.2 Solutions and Best Practices
Addressing common problems during overhaul involves replacing worn components, ensuring precise alignment, and using genuine Lycoming parts. Following the manual’s guidelines and documenting repairs is crucial. Regular inspection of cylinders and bearings, along with proper torque specifications, minimizes future issues. Consulting experienced mechanics for complex repairs and conducting thorough post-overhaul testing ensures reliability and safety, adhering to FAA standards and extending engine lifespan.
Cost and Time Considerations
The Lycoming IO-360 overhaul cost typically ranges from $20,000 to $30,000, depending on parts and labor. Completion time averages 4-6 weeks, varying by shop workload and engine condition.
7.1 Estimated Cost of Overhaul
The estimated cost for overhauling a Lycoming IO-360 engine typically ranges between $20,000 and $30,000. This includes parts and labor, with parts alone costing around $10,000 to $15,000. Labor costs vary depending on the shop’s rates and the engine’s condition. Additional expenses may arise from unforeseen repairs or upgrades, making it essential to budget accordingly; Costs can fluctuate based on regional labor rates and specific overhaul requirements.
7.2 Time Requirements for Completion
The Lycoming IO-360 overhaul typically requires 60 to 100 hours of labor, depending on the shop’s experience and the engine’s condition. Disassembly, inspection, and reassembly are time-intensive processes. Additional time may be needed for parts procurement and machining. Shops often quote 2 to 4 weeks for completion, ensuring thoroughness and adherence to FAA standards. Proper planning is crucial to minimize downtime and ensure the engine is airworthy upon completion.
Modifications and Upgrades
Popular modifications for the Lycoming IO-360 include fuel injection system upgrades, ignition enhancements, and cylinder improvements. These upgrades can boost performance, efficiency, and reliability, though they may increase maintenance complexity and cost. Always ensure modifications comply with FAA regulations and are performed by certified professionals to maintain airworthiness and safety standards.
8.1 Popular Modifications for the Lycoming IO-360
Popular modifications for the Lycoming IO-360 include crankshaft grinding, fuel injection system upgrades, and ignition enhancements like Lightspeed ignition. Nickel-plated cylinders and performance-enhancing cylinder kits are also common. Additionally, some owners opt for lightweight components or improved cooling systems to enhance efficiency and durability. These modifications aim to optimize engine performance while maintaining compliance with FAA standards and ensuring reliable operation.
8.2 Impact on Performance and Maintenance
Modifications like fuel injection upgrades and ignition enhancements can improve power output and fuel efficiency. Lightweight components and improved cooling systems enhance performance while maintaining reliability. However, these upgrades may require more frequent inspections and specialized maintenance. Owners must ensure all modifications comply with FAA standards to avoid compliance issues and maintain airworthiness. Proper documentation and adherence to maintenance schedules are crucial for long-term engine health and performance;
Regulatory Compliance
Adhering to FAA standards and guidelines ensures airworthiness and operational safety. Proper documentation and compliance with overhaul manual specifications are essential for maintaining regulatory approval and avoiding violations.
9.1 FAA and Other Regulatory Requirements
Compliance with FAA regulations is critical for the Lycoming IO-360 engine overhaul. Adhering to Part 43 and Part 145 guidelines ensures airworthiness and operational safety. The overhaul process must follow the approved manual, and all modifications must meet FAA standards. Proper documentation and certification are required to maintain regulatory compliance and ensure the engine meets safety and performance criteria. Regulatory oversight guarantees adherence to industry standards.
9.2 Documentation and Record-Keeping
Accurate documentation is essential during the Lycoming IO-360 overhaul. Detailed records of parts replaced, inspections, and repairs must be maintained. Logbook entries and compliance documentation ensure traceability and adherence to regulatory standards. Proper record-keeping facilitates future maintenance planning and verifies the engine’s airworthiness. All documentation must align with FAA guidelines and be stored securely for audit purposes and long-term reference. Thorough records ensure transparency and accountability throughout the overhaul process.
The Lycoming IO-360 overhaul is a critical process requiring precision, adherence to manuals, and proper documentation. Regular maintenance ensures safety, performance, and compliance with aviation standards, guaranteeing reliable engine operation.
10.1 Summary of Key Points
The Lycoming IO-360 overhaul process requires precision, adherence to the manual, and proper documentation. Regular maintenance ensures safety, performance, and compliance with aviation standards. Key steps include inspection, disassembly, replacement of worn parts, and thorough testing. Troubleshooting common issues and following best practices are essential for a successful overhaul. Proper tools, workspace preparation, and adherence to guidelines ensure the engine’s longevity and reliability.
10.2 Final Tips for a Successful Overhaul
Adhere strictly to the Lycoming IO-360 overhaul manual and use approved tools to ensure precision. Maintain a clean, organized workspace to prevent contamination or loss of parts. Consult experienced professionals if unsure about complex procedures. Document every step for future reference and regulatory compliance. Conduct thorough post-overhaul checks and follow break-in procedures to ensure optimal engine performance and longevity.
Plan for the estimated time and cost, and prioritize safety throughout the process. Regular maintenance after overhaul will sustain the engine’s reliability and efficiency, ensuring compliance with aviation standards and enhancing overall aircraft performance. Continuous vigilance and adherence to best practices are key to a successful overhaul and safe flight operations.